Understanding the Basics and Applications of Plastic Extrusion in Modern Production
In the world of modern-day production, the strategy of plastic extrusion plays a crucial duty - plastic extrusion. This detailed process, entailing the melting and shaping of plastic with specialized dies, is leveraged throughout various markets for the development of varied items. From auto components to consumer goods product packaging, the applications are vast, and the possibility for sustainability is equally impressive. Deciphering the principles of this procedure reveals the real flexibility and possibility of plastic extrusion.
The Principles of Plastic Extrusion Refine
While it may appear facility, the principles of the plastic extrusion procedure are based on relatively uncomplicated principles. It is a manufacturing process where plastic is melted and then formed into a continuous account with a die. The plastic extrusion process is extensively made use of in numerous markets due to its versatility, cost-effectiveness, and efficiency.
Various Kinds of Plastic Extrusion Techniques
Building upon the standard understanding of the plastic extrusion procedure, it is required to discover the different strategies entailed in this manufacturing method. In comparison, sheet extrusion produces large, level sheets of plastic, which are usually additional processed into items such as food product packaging, shower curtains, and vehicle parts. Recognizing these strategies is vital to using plastic extrusion successfully in modern-day manufacturing.
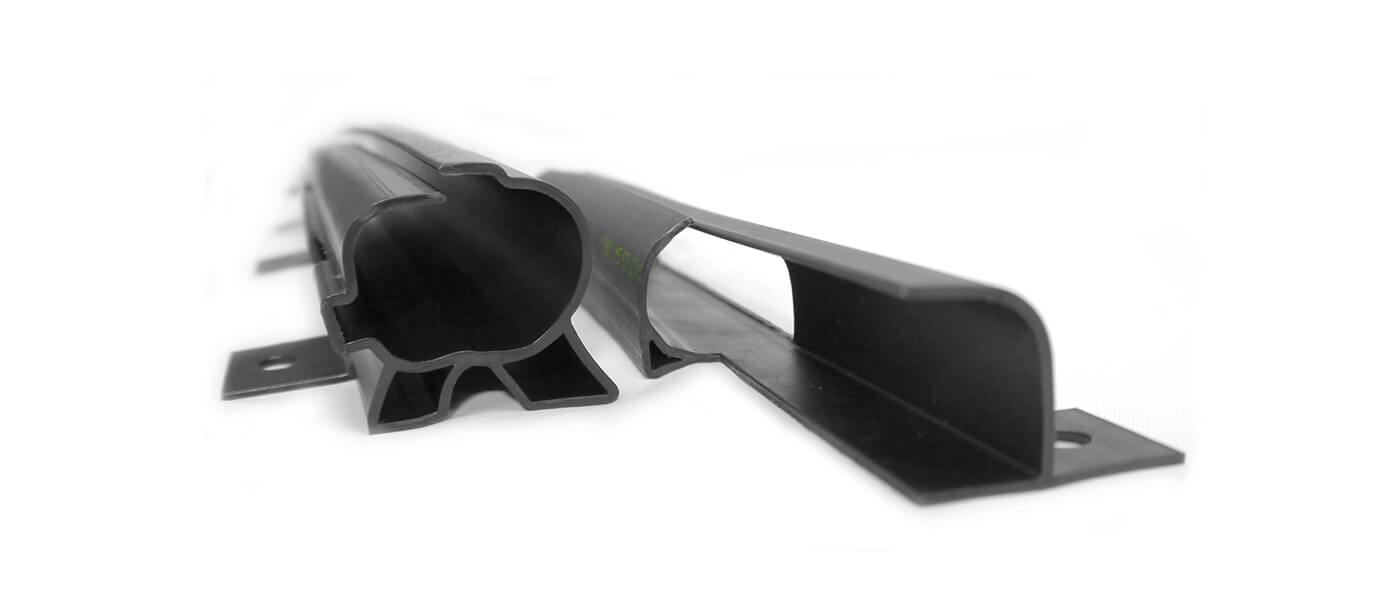
The Duty of Plastic Extrusion in the Automotive Market
A frustrating bulk of components in contemporary automobiles are items of the plastic extrusion procedure. Plastic extrusion is mainly utilized in the production of numerous vehicle elements such as bumpers, grills, door panels, and control panel trim. Hence, plastic extrusion plays a critical duty in automotive manufacturing.
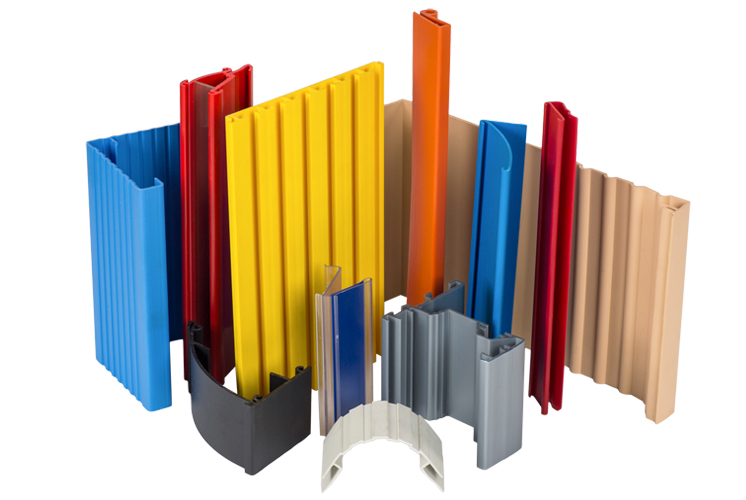
Applications of Plastic Extrusion in Customer Goods Production
Past its significant effect on the automobile market, plastic extrusion proves similarly efficient in the realm of durable goods making. This process is essential in developing a vast selection of items, from food product packaging to house devices, playthings, and also medical tools. The adaptability of plastic extrusion enables producers see post to design and create complex shapes and sizes with high precision and performance. In addition, as a result of the recyclability of many plastics, squeezed out elements can be recycled, lowering waste and price. The flexibility, adaptability, and cost-effectiveness of plastic extrusion make it a recommended option for many durable goods suppliers, contributing substantially to the industry's development and development. However, the ecological ramifications of this widespread use need cautious factor to consider, a topic to be discussed better in the subsequent area.
Ecological Influence and Sustainability in Plastic Extrusion
The prevalent usage of plastic extrusion in making welcomes scrutiny of its ecological internet implications. Efficient equipment reduces energy use, while waste monitoring systems reuse scrap plastic, decreasing raw product demands. Despite these improvements, even more technology is needed to alleviate the environmental impact of plastic extrusion.
Verdict
In verdict, plastic extrusion plays a critical function in contemporary manufacturing, specifically in the automobile and durable goods fields. Its flexibility permits for the production of a variety of elements with high precision. In addition, its read this post here capacity for reusing and advancement of biodegradable products supplies a promising avenue towards sustainable techniques, thereby resolving environmental worries. Understanding the essentials of this process is vital to maximizing its advantages and applications.

The plastic extrusion procedure is extensively made use of in numerous markets due to its convenience, effectiveness, and cost-effectiveness.
Building upon the standard understanding of the plastic extrusion process, it is essential to explore the numerous methods involved in this manufacturing technique. plastic extrusion. In contrast, sheet extrusion produces large, level sheets of plastic, which are generally further refined right into products such as food product packaging, shower drapes, and cars and truck parts.A frustrating majority of parts in modern-day automobiles are items of the plastic extrusion process
Comments on “Plastic extrusion for streamlined, scalable manufacturing solutions”